Chiller Van Load Capacity: What You Need to Know
When transporting temperature-sensitive goods, understanding chiller van load capacity is crucial for efficiency and safety. This article will define load capacity, explain how to calculate it, and highlight the significance of choosing the right chiller van. Readers will learn how to ensure they meet transportation requirements while avoiding issues such as overloading, which can lead to costly delays or product loss. By grasping these key points, businesses can improve their logistics and maintain the quality of their perishable items.
Define Chiller Van Load Capacity

Understanding chiller van load capacity involves several crucial aspects. Key factors influencing capacity include the type of goods being transported, as shelf life varies between products. Different types of chiller vans offer varying capacities, each tailored to specific supply chain needs. Additionally, legal regulations play a significant role in load limits, impacting how businesses manage their cold chain logistics effectively.
Key Factors Influencing Load Capacity
The load capacity of a chiller van is significantly impacted by the type of goods being transported. For instance, perishable items such as fresh produce or pharmaceuticals require precise temperature control to maintain their integrity during transport. To ensure the right conditions are met, reliable refrigeration systems like Thermo King units are essential, as they provide the necessary cooling capabilities tailored to different load types.
Another important factor to consider is the van‘s towing capabilities. The overall limit for how much weight a chiller van can carry includes the vehicle’s own weight and the additional load being towed if applicable. It is crucial for businesses to understand the towing specifications and steering capabilities of their chiller vans to prevent overloading, which can lead to mechanical failures or inefficient operations.
Legal regulations also have a direct influence on load capacity. Different regions may have specific regulations regarding carbon emissions, demanding that vehicles comply with environmental standards. Businesses must stay informed about the legal limits pertinent to their zip code to ensure their operations align with local laws, thereby safeguarding their logistics processes and promoting sustainability in cold chain transport.
Types of Chiller Vans and Their Capacities
Chiller vans come in various types, each designed to handle specific loads and meet diverse business requirements. For instance, standard refrigerated vans typically have a load capacity ranging from one ton to several tons, making them suitable for transporting fresh produce and dairy products. Their design facilitates optimal airflow, ensuring that temperature-sensitive items remain within safe limits during transport.
Refrigerated trailers, on the other hand, provide a larger capacity option for businesses needing to move bulk quantities of perishable goods. These trailers can accommodate loads exceeding ten tons, depending on their size and configuration. Equipped with advanced refrigeration systems, they maintain consistent temperatures, which is crucial for preserving product quality over long distances.
It is essential to consider the vehicle’s fuel tank capacity when selecting a chiller van. A larger fuel tank is beneficial for longer journeys, as it reduces the need for frequent stops and ensures that the refrigeration unit operates efficiently. Moreover, the vehicle’s transmission type can influence its towing capabilities, affecting how much load it can safely transport without compromising performance.
Legal Regulations Affecting Load Limits
Legal regulations play a crucial role in defining the load limits of chiller vans. Specific guidelines established by transportation authorities help ensure safe transport of goods, particularly perishable items like meat. These regulations may dictate weight limits per axle, which directly affects the total load a chiller van can transport without compromising safety or efficiency.
Another important consideration is the vehicle’s engine and brake specifications. Regulations often require that vehicles meet stringent safety standards, including those related to braking systems and engine performance. A well-maintained engine and effective brakes are essential for handling the loads safely, especially when transporting heavy freight over long distances.
Additionally, compliance with environmental regulations can influence load limits. In many regions, laws regarding fuel tank capacities are established to minimize carbon emissions. For chiller vans, this means ensuring that the fuel tank is large enough to support efficient operations while adhering to these standards, allowing for uninterrupted runs when transporting temperature-sensitive products.
Calculate Your Chiller Van Load Capacity

Understanding volume and weight measurements is essential for calculating the load capacity of a chiller van. This section outlines the necessary steps to accurately determine capacity and highlights common mistakes that can occur during the calculation process. By focusing on aspects such as wheelbase length, steel frame structure, and the influence of a spare tire, businesses can ensure optimal refrigerated transport operations.
Understanding Volume and Weight Measurements
Calculating the load capacity of a refrigerated van requires a solid understanding of both volume and weight measurements. The weight of the goods must align with the van’s specifications to ensure safe transportation, especially when considering the different types of perishable items. For businesses utilizing a chiller van for rent in dubai, maintaining proper sanitation is critical as it guarantees the quality and safety of the products being transported while adhering to local regulations.
The door dimensions of a chiller van also play a vital role in assessing its load capacity. Ensuring that the items can fit through the doors without issue is essential for efficient loading and unloading processes. By carefully measuring the height, width, and depth of the van‘s interior, operators can maximize the use of space and ensure optimal conditions for maintaining temperature-sensitive products throughout the transport journey.
Understanding weight distribution is equally important when calculating the chiller van‘s load capacity. Properly balancing the load helps prevent issues such as instability and excessive strain on the vehicle. Businesses should consider the overall weight and ensure that heavier items are secured properly, as this not only enhances safety but also upholds the integrity of goods stored in the refrigerated environment.
Steps to Calculate Your Load Capacity
To accurately determine the load capacity of a chiller van, one must first assess the total weight of the cargo and its compatibility with the van‘s specifications. This begins with calculating the weight of the goods being transported, ensuring that the combined weight aligns with the van‘s maximum load capability. For example, knowing the weight of the compressor and refrigerant used in the refrigeration system can help gauge how much additional cargo can be added without exceeding limits.
Next, it is essential to consider the internal dimensions of the van, including the space available for insulation materials like fiberglass, which contributes to maintaining the cold environment. By measuring the height, width, and depth within the van, operators can better understand how to maximize space for cargo placement. This step is crucial for ensuring that temperature-sensitive items are stored efficiently and remain within safe temperature ranges during transport.
Finally, weight distribution plays a key role in calculating load capacity. Even if the total weight fits within the van’s limits, improper distribution can cause handling issues or damage to refrigeration equipment. Businesses must ensure that heavier items are strategically placed and secured to prevent shifts during transit, which could impact the performance of the compressor and overall refrigeration system efficacy.
Common Mistakes in Calculation
One common mistake when calculating chiller van load capacity is failing to account for the weight of the refrigeration system itself. For example, whether utilizing an electric battery or a diesel engine, the weight of these components can significantly reduce the total cargo capacity available for inventory. Businesses must always consider how the additional weight from the refrigeration unit impacts the overall load restrictions of the van to avoid overloading.
Another frequent oversight involves neglecting to evaluate the operational features of the van, such as the tail lift and airbag systems. These features can add weight and affect how much cargo can be safely transported. Understanding these elements is essential to determine usable space accurately and maintain effective logistics processes while ensuring compliance with regulations.
Lastly, improper weight distribution is a critical mistake that can compromise both safety and efficiency. Even with accurate calculations, if heavier items are poorly placed, it may lead to instability or potential damage to the refrigeration system. Properly securing cargo within the van and adhering to weight distribution guidelines, particularly around sensitive components such as the airbag system, ensures safer transportation and preserves the integrity of perishable goods.
Importance of Load Capacity in Transportation

Understanding load capacity is essential for operational efficiency in refrigerated transport. Failure to adhere to weight limits can lead to increased costs, including potential fines for exceeding vehicle weight regulations and higher fuel consumption due to added strain. Moreover, maintaining proper load capacity is crucial to ensure product quality during transit, as improper weight distribution may compromise the integrity of temperature-sensitive goods. Each aspect plays a critical role in efficient logistics and the overall success of cold chain management.
Impact on Operational Efficiency
Load capacity has a significant impact on the overall operational efficiency of chiller transport. Overloading a box truck can result in increased pressure on the axles, potentially leading to mechanical failures and a warranty void. Maintaining compliance with load limits helps prevent these issues and ensures that vehicles perform optimally, minimizing downtime and costly repairs.
Proper weight distribution within the chiller van is vital for effective manufacturing of cold chain logistics. When loads are balanced, it enhances stability and driving control, which is essential for transporting perishable goods safely. Businesses that prioritize load capacity not only protect their products but also support their drivers in managing vehicles under safe operating conditions.
Moreover, understanding how load capacity corresponds with transportation costs is crucial. Exceeding recommended weights can lead to higher fuel consumption due to increased strain on the engine. By adhering to established load capacities, companies can optimize their logistics operations, ensuring they maximize efficiency and maintain a competitive edge in the market.
Cost Implications of Exceeding Capacity
Exceeding the load capacity of a chiller van can lead to significant financial repercussions. Overloading a vehicle often results in increased fuel consumption, as the engine must work harder to support the added weight. This added strain can inflate operational expenses over time, affecting overall profitability for businesses relying on cold chain logistics.
Moreover, exceeding weight limits can compromise the vehicle’s performance, particularly components like the power steering system. When a van operates outside its designated capacity, the power steering may struggle to function effectively, leading to difficulties in maneuvering and potential mechanical failures. Such issues can necessitate costly repairs and a loss of productivity while the vehicle is out of service.
In addition to direct costs related to repairs and fuel, businesses face the risk of fines for violating weight restrictions enforced by local authorities. These penalties, combined with increased liability insurance premiums due to the higher risk of accidents, create a financial burden that can impact a company’s bottom line. Understanding the implications of exceeding capacity is essential for maintaining a sustainable and cost-effective operation in refrigerated transport.
Ensuring Product Quality During Transit
Maintaining product quality during transit relies heavily on respecting the load capacity of a chiller van. Overloading can lead to fluctuations in temperature, which directly impacts the integrity of perishable goods like dairy, meat, and pharmaceuticals. Understanding the specifications of the chiller van allows businesses to securely transport their products while ensuring they remain within the optimal temperature range.
Proper weight distribution is another critical factor that influences product quality. When products are evenly balanced within the chiller van, it helps preserve the refrigeration system’s functionality, reducing the risk of temperature drops or spikes. This balance protects temperate-sensitive items from potential damage during movement, thus maintaining their quality from the point of origin to the destination.
Implementing effective monitoring systems within the chiller van can further enhance product quality assurance. Climate-controlled technologies, such as temperature logging devices, enable real-time tracking of the environment inside the vehicle. By ensuring that the conditions remain consistent and safe throughout the transit journey, businesses can confidently deliver their goods while upholding standards expected in industries such as food service and healthcare.
Factors Affecting Chiller Van Load Capacity

Temperature control requirements are crucial for maintaining the integrity of goods during transportation, particularly for sensitive items. The type of packaging used can also impact load capacity, influencing how well products are protected and stored. Additionally, space optimization strategies play a vital role in maximizing the van‘s interior, ensuring efficient use of available space while adhering to load limits. Each of these factors is essential for effective cold chain logistics.
Temperature Control Requirements
Temperature control is a fundamental requirement that directly impacts chiller van load capacity. Each type of product transported has specific temperature needs that must be consistently maintained to ensure quality. For instance, pharmaceuticals and fresh produce often require precise temperature settings to prevent spoilage, which can restrict the overall weightload of a chiller van. Businesses must choose refrigeration systems equipped to handle these demands efficiently, ensuring the loaded items remain within safe temperature thresholds.
The insulation properties of the chiller van also play a crucial role in temperature control. Proper insulation minimizes fluctuations in the internal environment, which is vital for preserving the quality of temperature-sensitive goods. A well-insulated chiller van can support a stable temperature, allowing businesses to maximize their load capacity while adhering to safety standards in cold chain logistics.
Regular maintenance of the refrigeration systems is essential for effective temperature control. This involves checking the functionality of compressors and monitoring cooling performance. By ensuring that these systems operate at peak efficiency, businesses can avoid the risk of temperature-related spoilage, thus protecting their investments in perishable goods. This proactive approach contributes to optimal load capacity management, enhancing overall delivery reliability.
Packaging Types and Their Effects
The type of packaging used for products transported in chiller vans directly influences load capacity and effectiveness in maintaining optimal temperature. For example, rigid containers that securely hold products can maximize space and prevent movement during transit. This stability is essential for maintaining the integrity of temperature-sensitive items, thereby preventing spoilage and ensuring product quality.
Flexible packaging, while lightweight and space-efficient, may not provide the same level of protection from temperature fluctuations as more rigid alternatives. Businesses should consider factors such as insulation properties and sealing efficiency when selecting packaging materials for refrigerated transport. Choosing the right combination can significantly enhance load capacity and product preservation during delivery.
Moreover, sustainable packaging solutions are gaining attention in the industry, providing environmentally friendly options without compromising performance. By utilizing renewable materials or reducing excess packaging, companies can optimize their chiller van load capacity while appealing to eco-conscious consumers. This dual advantage not only supports compliance with regulations but also addresses the growing demand for sustainability in cold chain logistics.
Space Optimization Strategies
To maximize the load capacity of a chiller van, careful consideration of space optimization strategies is essential. Utilizing vertical space can greatly enhance the amount of product transported. Businesses should consider adjustable shelving or stackable containers that facilitate better organization and allow for efficient use of available height within the van.
Another effective strategy involves ensuring that loads are evenly distributed throughout the chiller van. Proper placement of items can prevent unnecessary movement during transit, which reduces the risk of spoilage for temperature-sensitive goods. By strategically placing heavier items at the bottom and lighter ones on top, businesses can maintain stability while effectively utilizing all available space.
Employing packaging solutions that are both space-efficient and insulative can further support load optimization. For instance, selecting vacuum-sealed or compact packaging options not only saves space but also helps maintain the required temperature for perishable products. Businesses that focus on these thoughtful packing methods can transport more goods while adhering to safety and quality standards, ultimately enhancing their cold chain logistics operations.
Selecting the Right Chiller Van

Analyzing business needs is crucial when selecting the right chiller van, as different operations require specific features and capacities. Comparing various models and specifications can help identify options that best suit those needs. Additionally, choosing a reliable provider ensures access to quality vehicles and support, ultimately enhancing cold chain logistics and operational efficiency.
Analyzing Your Business Needs
When evaluating business needs, understanding the specific goods to be transported is crucial. Different products, such as pharmaceuticals or fresh produce, have unique temperature control requirements, which directly influence the choice of chiller van. Companies must assess the nature of their inventory to select a van that can maintain the proper load capacity and temperature during transit.
Another factor to consider is the volume of goods needing transportation on a regular basis. Businesses that transport large quantities regularly may benefit from larger refrigerated vans or trailers to enhance efficiency. Analyzing delivery frequency and amounts can guide operators in selecting a vehicle that optimally supports their logistics operations, ensuring timely service without compromising product integrity.
Finally, it is vital for companies to consider operational costs. The right chiller van not only meets load capacity requirements but also aligns with budgetary constraints. Businesses should evaluate fuel efficiency, maintenance costs, and rental prices to make an informed decision that maximizes value while meeting their cold chain logistics demands effectively.
Comparing Different Models and Specs
When comparing different chiller van models and specifications, businesses should focus on the specific load capacities offered by each option. Some models are designed for lighter loads and shorter distances, while others are built for heavy-duty applications requiring larger capacities and extended refrigeration capabilities. Understanding these distinctions helps ensure that companies select the right vehicle for their cold chain transport needs, enhancing efficiency and product safety.
Moreover, evaluating the features of each model, such as the refrigeration technology and insulation properties, is critical for maintaining optimal temperature control. Advanced systems, like those equipped with digital thermostats, provide real-time monitoring, which is essential for sensitive items like pharmaceuticals. By considering these features, businesses can make informed decisions that align with their operational requirements and ensure compliance with industry standards.
Lastly, assessing the overall size and layout of the chiller vans can significantly impact loading and unloading processes. Models with wider doors and more spacious interiors allow for easier access, reducing the handling time and potential for product damage. By prioritizing these practical aspects, companies can improve their logistics operations and maintain the quality of their temperature-sensitive goods throughout the transport journey.
Tips for Choosing a Reliable Provider
When selecting a reliable provider for chiller vans, businesses should prioritize companies with a strong reputation in the logistics industry. A provider’s track record in offering high-quality refrigerated transport solutions speaks volumes about their reliability and commitment to service. Researching online reviews and seeking recommendations from peers can help identify providers that consistently meet customer expectations.
Another critical factor in choosing a dependable provider is evaluating their fleet’s condition and technology. Providers that invest in modern refrigeration systems demonstrate a commitment to maintaining optimal temperature control for perishable goods during transport. Furthermore, companies that offer regular maintenance checks on their vehicles ensure that the chiller vans are consistently functioning at peak efficiency, minimizing the risk of cargo spoilage.
Lastly, businesses should inquire about the level of customer support provided by the rental company. A responsive provider that offers guidance and assistance throughout the rental process can make a significant difference in ensuring smooth logistics operations. Clear communication regarding load capacity, transportation needs, and any potential challenges can foster a productive partnership, ultimately enhancing the overall effectiveness of cold chain management.
Frequently Asked Questions About Chiller Van Load Capacity
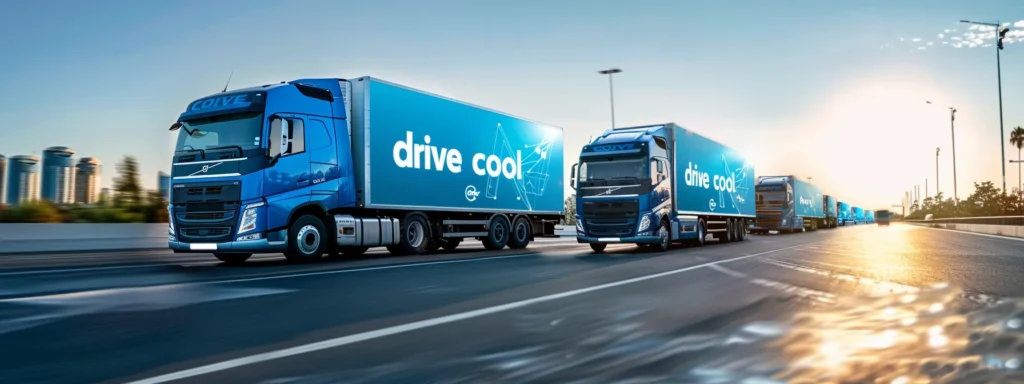
Addressing chiller van load capacity involves understanding key concepts such as actions to take if cargo exceeds capacity, strategies for optimizing space for different products, and best practices for loading and unloading sensitive items. These insights are crucial for maintaining product quality and ensuring compliance with cold chain logistics, enabling businesses to transport their goods effectively and safely.
Each of these topics provides valuable information to help companies navigate the challenges associated with transporting perishable items, ensuring that they can uphold the integrity of their temperature-sensitive products throughout the logistics process.
What to Do if Your Cargo Exceeds the Capacity?
When cargo exceeds the load capacity of a chiller van, the first step is to reassess the items being transported. Businesses should evaluate which products are essential for immediate delivery and prioritize those while leaving excess items behind. This strategy not only helps maintain compliance but also ensures that the remaining cargo is transported under optimal conditions.
Next, organizations should consider splitting the delivery across multiple trips or utilizing additional vehicles. This approach allows for efficient management of the load without compromising safety or product quality. By properly scheduling workloads, companies can maintain their logistics operations and meet customer demands without the risk of overloading their refrigeration units.
Lastly, investing in a comprehensive understanding of load specifications is critical. Training staff about how to identify and manage load capacity can prevent future issues. Regular monitoring of cargo weight and distribution is essential for effective cold chain logistics, ensuring that temperature-sensitive items remain safe during transport while adhering to legal requirements.
How to Optimize Space for Various Products?
To optimize space for various products in a chiller van, businesses should first focus on understanding the dimensions and weight of the items being transported. Cleverly arranging items based on their size and weight can significantly enhance the use of interior space. For instance, heavier products should be placed at the bottom to create a stable base, while lighter items can occupy the upper sections, ensuring that the load is well-balanced during transport.
Utilizing appropriate packaging plays a critical role in maximizing space efficiency. Packaging that fits snugly can help prevent movement during transit, which is essential for maintaining the quality of temperature-sensitive goods. Companies might consider using stackable containers or vacuum-sealed packages that save space while enhancing insulation, thus ensuring products remain at the necessary temperatures.
Incorporating organization strategies, such as labeling and categorizing items, can streamline the loading and unloading process. By clearly identifying each product and its required temperature conditions, drivers can manage their loads more effectively. This method not only maximizes space but also enhances operational efficiency, positively impacting the cold chain logistics overall.
Best Practices for Loading and Unloading Sensitive Cargo
Loading and unloading sensitive cargo in a chiller van demands meticulous attention to detail to maintain product integrity. Operators should begin by ensuring that the van’s temperature settings are optimal before introducing any perishable items. This proactive step prevents shocks to the system and helps preserve the quality of temperature-sensitive goods during transport.
Proper training for staff involved in handling sensitive cargo is crucial. Workers should be aware of load limits, the importance of securing items, and the correct handling procedures. For instance, using protective coverings or padded containers can prevent damage during loading and unloading, which is essential when dealing with delicate products such as pharmaceuticals or fresh produce.
Effective organization during these processes enhances efficiency and minimizes risks. Labeling items based on temperature requirements and handling instructions ensures that all personnel can manage loads appropriately. By fostering a structured environment, businesses can streamline operations and uphold the quality of their products throughout the logistics process, ensuring that cold chain standards are consistently met.
Conclusion
Understanding chiller van load capacity is vital for businesses engaged in transporting perishable goods. Proper load management ensures compliance with legal regulations, maintains product quality, and enhances operational efficiency. By effectively utilizing space, optimizing weight distribution, and selecting the right van, companies can safeguard their logistics processes. Prioritizing these aspects not only protects investments in temperature-sensitive products but also strengthens overall cold chain management.