Chiller Truck Tail Lift Capacity Explained
Chiller truck tail lifts play a crucial role in the transportation of temperature-sensitive goods, yet many businesses underestimate their capacity needs. This article will clarify what tail lift capacity is, the factors influencing it, and how to evaluate the right size for your requirements. By understanding these aspects, readers can ensure efficient loading and unloading, ultimately enhancing their logistics operations. This content will address common concerns regarding capacity limitations and provide best practices for maximizing the effectiveness of chiller truck tail lifts, ensuring goods arrive in optimal condition.
Chiller Truck Tail Lift Capacity Overview
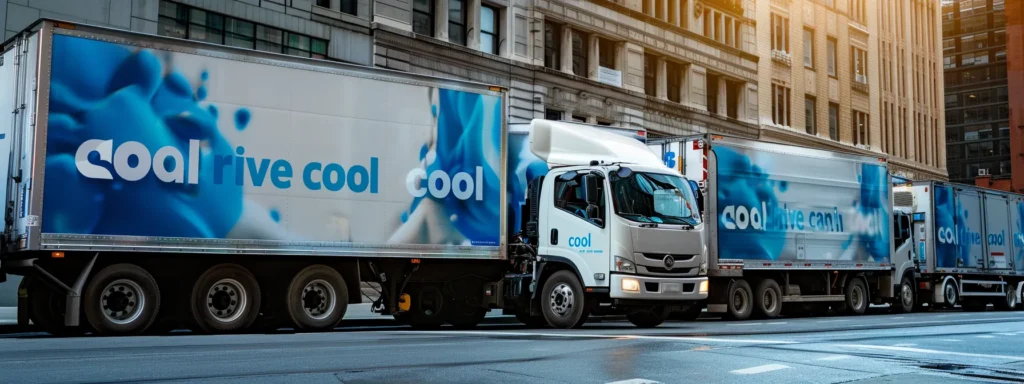
Understanding tail lift weight limitations is crucial for optimizing **chiller truck with tail lift** operations. The capacity of these lifts directly impacts the efficiency of cold chain logistics, ensuring temperature-sensitive goods are transported safely. Common applications for chiller truck tail lifts include the delivery of perishables, pharmaceuticals, and fuel tanks, where the hydraulic cylinder plays a significant role in facilitating smooth loading and unloading. Each of these elements will be explored in detail in the following sections.
Understanding Tail Lift Weight Limitations
Understanding tail lift weight limitations is essential for optimizing the operations of chiller trucks. These hydraulic systems are designed to handle specific weights, which directly impacts the efficiency and safety of loading and unloading temperature-sensitive products. For instance, when transporting heavy items like tanks, ensuring that the tail lift does not exceed its maximum capacity is crucial to prevent mechanical failure and ensure smooth operations.
Vehicles like box trucks equipped with tail lifts require careful attention to axle load distribution. This means that the weight placed on the tail lift should be appropriately distributed across the axles to maintain control and stability during transit. An imbalance could lead to safety hazards, especially when maneuvering in tight spaces or making sudden stops, which underscores the importance of adhering to established weight restrictions.
Incorporating automatic transmission in chiller trucks can further enhance efficiency when using tail lifts. The seamless operation of these vehicles allows for better control while handling heavy loads, such as pharmaceuticals and food products. A well-maintained tail lift system, combined with appropriate vehicle specifications, ensures that businesses can transport their perishable goods safely and efficiently, addressing key operational concerns.
Importance of Capacity in Cold Chain Logistics
The capacity of chiller truck tail lifts plays a vital role in cold chain logistics, significantly influencing the efficiency of transporting temperature-sensitive goods. With the ability to handle varying payloads, these systems ensure that products ranging from pharmaceuticals to perishables remain in optimal condition during transit. For instance, when dealing with a fiberglass tanker delivery, understanding how to maximize tail lift capacity is essential for safe and effective loading.
Moreover, the design and weight distribution of chiller trucks, including their roof and tail lift systems, must be carefully considered to maintain control and safety while steering. An appropriately balanced load not only facilitates smoother operations but also minimizes wear on the vehicle. This balance is crucial for cold chain logistics, where timing and temperature consistency are paramount.
By effectively managing tail lift capacity, businesses can enhance their logistics strategies, leading to better inventory turnover and reduced spoilage of goods. The right chiller truck setup allows operators to maximize efficiency, ensuring that all temperature-sensitive deliveries are made promptly and safely, addressing the critical needs of businesses that depend on reliable transportation solutions.
Common Applications for Chiller Truck Tail Lifts
Chiller trucks with tail lifts are essential for transporting a variety of temperature-sensitive goods. Common applications include the delivery of fresh produce, where maintaining a specific liquid temperature is vital to preserving quality. The tail lift enables seamless loading and unloading, accommodating varying vehicle weight safely and efficiently.
In pharmaceuticals, chiller truck tail lifts play a crucial role in ensuring that sensitive medications are delivered without temperature fluctuations. These vehicles can maintain a vacuum environment during transit, protecting the integrity of the products. The precision of tail lifts allows for careful handling of both light and heavy cargo, tailored to the necessary weight restrictions.
Food service businesses frequently utilize chiller trucks with tail lifts to manage their cold chain logistics effectively. By delivering bulk items quickly and securely, these vehicles prevent spoilage and enhance the efficiency of supply chains. The adjustable capacity of a tail lift makes it easier for operators to ship diverse items, ensuring that all deliveries meet stringent temperature requirements.
Factors Influencing Chiller Truck Tail Lift Capacity

The type of tail lift and its specifications directly affect a chiller truck’s capacity, impacting loading efficiency and safety. Vehicle size and design considerations also play a crucial role in determining lift performance. Moreover, adherence to regulatory standards ensures compliance across international trade, thus influencing operational practices, energy consumption, and transmission systems. Each of these factors contributes to optimizing logistics for temperature-sensitive goods.
Type of Tail Lift and Its Specifications
The type of tail lift installed on a chiller truck significantly determines its load capacity and operational efficiency. Commonly, tail lifts can be categorized into column lifts, tuckaway lifts, and platforms, each with distinct specifications tailored for various applications. For instance, a flatbed truck might utilize a column lift for heavy machinery transport, while a tuckaway lift is ideal for urban deliveries requiring space-saving designs.
Specifications also encompass weight limits and hydraulic performance, impacting the cost efficiency of logistics operations. An airbag suspension system can enhance ride stability and load distribution, which is particularly beneficial when transporting sensitive items in chiller trucks. Businesses involved in exporting goods, especially in the mining or agricultural sectors, must evaluate tail lift specifications to ensure alignment with their delivery needs and compliance with international standards.
In addition, the tail lift‘s design affects loading and unloading speed, critical factors for businesses with tight delivery timelines. The pricing of tail lifts varies based on their complexity and capabilities; thus, understanding these specifications allows companies to make informed purchasing decisions. By selecting the appropriate tail lift type, operators in cold chain logistics can better meet their performance requirements, ultimately improving service delivery and customer satisfaction.
Vehicle Size and Design Considerations
The size and design of chiller trucks significantly influence the operational capacity of tail lifts. A larger vehicle often requires a stronger tail lift to accommodate heavier loads, which necessitates higher horsepower for efficient lifting and transportation. Additionally, robust materials such as steel are essential to ensure durability and longevity, allowing the tail lift to function effectively under various conditions while maintaining safety standards.
Manufacturing practices also play a critical role in determining how well a tail lift integrates with the overall vehicle design. Customized installations may enhance the vehicle’s weight distribution, which is vital for stable operation. By aligning the tail lift specifications with the truck’s dimensions, businesses can enhance performance, leading to safer and more effective load handling during deliveries.
When navigating customs regulations, adhering to design considerations is particularly important for international operations. Certain specifications may be necessary to meet import/export standards, affecting the overall logistics strategy. Choosing the right tractor and tail lift combination can facilitate seamless transitions through customs, reducing delays and ultimately enhancing efficiency in transporting temperature-sensitive goods.
Regulatory Standards and Compliance
Regulatory standards play a significant role in shaping the operational capacity of chiller truck tail lifts. Compliance with these standards ensures that vehicles meet safety requirements, particularly in terms of brake performance and maximum cargo height. For example, vehicles operating at ports must adhere to strict guidelines to prevent accidents, which includes ensuring that tail lifts are capable of handling expected loads without compromising safety.
The materials used in the construction of tail lifts must also comply with industry specifications to minimize wear and ensure durability during operation. Businesses transporting temperature-sensitive cargo need to be aware of these regulations to maintain not only the integrity of their goods but also the safety of the personnel involved in the loading and unloading processes. Meeting these standards helps to avoid costly fines and enhances operational efficiency.
Furthermore, regular assessments of tail lift performance against regulatory benchmarks help businesses optimize their logistics operations. By ensuring that tail lifts are properly calibrated for weight limits and height clearance, companies can improve delivery times and reduce the risk of damage to cargo. Staying informed about current regulations allows operators to make smarter decisions regarding equipment maintenance and upgrades, ultimately supporting smoother cold chain logistics.
Evaluating the Right Capacity for Your Needs

Assessing load types and volumes is crucial for selecting the appropriate capacity of a refrigerator truck‘s tail lift. Balancing efficiency and safety ensures that payloads, whether made of aluminium or polyurethane, are managed correctly. Seasonal changes can also impact the handling of temperature-sensitive goods, necessitating adjustments in tail lift specifications. These factors inform the decision-making process, enhancing operational effectiveness.
Understanding the interplay between different load requirements and material properties, including aluminium alloy components, aids logistics professionals in optimizing cold chain transport strategies. The following sections will delve deeper into these essential topics.
Assessing Load Types and Volumes
Assessing load types and volumes is fundamental in determining the appropriate capacity for chiller truck tail lifts. Different products have varying weight and size requirements, which impacts how they are loaded and transported through the cold chain. For example, when using a pallet jack to handle pallets of fresh produce, the weight distribution must be considered to ensure the tail lift can support the load without exceeding its limits.
Stainless steel containers are often chosen for their durability and ability to maintain temperature control during transport. Recognizing the specifics of these materials is essential for logistics experts, as improperly managed loads can lead to safety issues or product spoilage. Proper calculations, including the weight of the containers and the pallet itself, ensure a balanced and secure load, enhancing the overall efficiency of cold chain operations.
Understanding the nuances of different load types allows businesses to optimize their logistics strategies effectively. For instance, seasonal variations may affect product volumes, prompting adjustments in tail lift capacity requirements. By adapting their approach and considering factors such as load size and weight, companies can ensure their chiller trucks meet operational demands while maintaining safe transport conditions.
Balancing Efficiency and Safety
Balancing efficiency and safety in chiller truck tail lift operations is essential for ensuring that goods are transported securely and effectively. This consideration becomes particularly important when managing heavy loads, such as gasoline or diesel engine components, which require precise weight distribution to prevent accidents on the road. Operators must implement strategies that maximize payloads while adhering to safety protocols to maintain operational effectiveness.
The use of appropriate materials, such as foam insulation in cargo areas, aids in temperature control while also enhancing the overall balance of the load. Ensuring that all items are properly secured and placed within the tail lift‘s capacity not only optimizes performance but also minimizes risks during transit. Professionals must be vigilant about weight limits to prevent mechanical failures and guarantee smooth unloading processes.
Employing advanced monitoring systems can significantly enhance the balance between efficiency and safety. These systems provide real-time data on weight distribution and cargo conditions, allowing operators to make informed decisions while on the road. By understanding their tail lift capacity and monitoring critical factors, businesses can ensure that their operations run smoothly, ultimately improving delivery outcomes and customer satisfaction.
Considerations for Seasonal Changes
Seasonal changes significantly impact the logistics of chiller truck operations, especially regarding tail lift capacity. During warmer months, the increased temperature can affect the integrity of temperature-sensitive goods, necessitating a careful evaluation of payloads and machine performance. This means operators need to consider not only the weight limit but also how the heat may influence the cooling system and overall cargo stability.
Moreover, the dimensions of the cargo can vary seasonally, affecting how items are loaded and managed within the chiller truck. For instance, during peak seasons for fresh produce, the volume of goods may increase, requiring modifications in tail lift operations to accommodate heavier loads and maintain efficiency. Maintaining the right balance in loading during these times is crucial for ensuring safe and timely deliveries, thus enhancing overall operational effectiveness.
In addition to temperature fluctuations, different zip codes may require adjustments in logistics strategies, especially if local climates vary considerably. Operators must assess how seasonal factors affect delivery routes and equipment performance, adapting their tail lift capacity as necessary. This strategic planning ensures that businesses continue to meet customer demands while maintaining the safety and quality of their transported goods.
Best Practices for Using Chiller Truck Tail Lifts

Effective use of chiller truck tail lifts involves several best practices to ensure optimal performance in freight transport. Proper loading and unloading techniques are essential for maximizing capacity while minimizing risks. Regular maintenance tips can enhance the reliability of the tail lift, improving its operational efficiency. Additionally, training operators on the specific use of tail lifts ensures safe handling within factory and construction environments, contributing to a well-functioning chassis and brand reputation.
Loading and Unloading Techniques
Loading and unloading techniques play a crucial role in the efficient use of chiller truck tail lifts. Proper positioning of the vehicle, such as an Isuzu van with an appropriate wheelbase, can facilitate smoother operations. Keeping the loading area clear and organized allows loaders to perform tasks quickly and safely, reducing the risk of damage to both the goods and the truck.
Operators are encouraged to utilize appropriate air conditioning settings during the handling of temperature-sensitive products, ensuring that the environment remains optimal throughout the process. For example, cool air circulation helps maintain the integrity of pharmaceuticals and perishables, while effective loading techniques prevent temperature fluctuations that could jeopardize quality. By minimizing exposure to warm air during loading, businesses can enhance the overall effectiveness of their cold chain logistics.
Additionally, training staff on specific loading and unloading procedures for chiller trucks is vital for safety and efficiency. Ensuring that all team members understand the tail lift‘s weight capacity and proper handling of different types of cargo will prevent overloads and mechanical failures. With consistent practice and adherence to best practices, businesses can improve their operations, maintain product quality, and enhance customer satisfaction during the transportation of temperature-sensitive goods.
Maintenance Tips for Enhanced Capacity
Regular maintenance of the tail lift is essential to ensure optimal performance and extend its lifespan. Operators should conduct routine inspections to check for signs of wear and tear, including the hydraulic system, which plays a vital role in loading and unloading temperature-sensitive items such as meat. Ensuring all components function properly reduces the risk of breakdowns during operations, ultimately enhancing efficiency in cold chain logistics.
It’s important to keep the engine in peak condition, as it powers the tail lift operations. Regular oil changes and servicing not only allow the engine to function smoothly but also support the hydraulic system by providing adequate power when lifting heavy loads. A well-maintained engine prevents unexpected failures that could disrupt the transport of perishable goods and compromise their quality.
Operators should also be mindful of the tail lift‘s weight capacity and load distribution every time they handle meat and other heavy items. Properly securing and evenly distributing loads can significantly enhance the tail lift‘s capability, minimizing stress on the lift mechanics. By maintaining a focus on both routine servicing and load management, businesses can achieve greater efficiency in their logistics processes and ensure the integrity of their transported products.
Training for Operators on Tail Lift Use
Training for operators on tail lift use is essential for ensuring the safe and efficient operation of chiller trucks. Effective training programs should focus on familiarizing operators with the specific features and weight limitations of the tail lift system, as understanding its mechanics is vital in preventing overload and accidents. Practical demonstrations of loading and unloading techniques can reinforce this knowledge, helping operators feel confident in handling temperature-sensitive goods.
Operators must also learn the importance of maintaining optimal environmental conditions during loading operations; this includes understanding how to regulate temperature settings effectively. By ensuring that cool air circulates during loading, operators protect the integrity of pharmaceuticals and perishables. Additionally, role-playing scenarios can prepare operators for real-world challenges, enhancing their decision-making skills when faced with unexpected situations.
Regular assessments and refresher courses can help operators stay updated with the latest safety protocols and industry best practices. This ongoing education emphasizes the necessity of monitoring weight distribution and load management, which are critical components for successful tail lift operations. By investing in comprehensive training, businesses can foster a culture of safety, leading to smoother cold chain logistics and maintaining the quality of transported goods.
Innovations in Chiller Truck Tail Lift Technology

Recent advancements in weight management systems have revolutionized chiller truck tail lift operations, enhancing both efficiency and safety. Future trends in cold chain transportation indicate a shift towards smarter technologies and automation, making operations more streamlined. Case studies of successful implementations reveal practical insights into optimizing tail lift capacity, offering valuable strategies for businesses to improve their logistics performance.
Advancements in Weight Management Systems
Recent advancements in weight management systems significantly enhance the efficiency of chiller truck tail lifts. Modern technologies integrate real-time monitoring to assess load distribution, ensuring tail lifts operate within safe weight limits. This capability not only prevents mechanical failures but also optimizes overall logistics operations by minimizing the risks associated with overweight loads.
Implementing smart sensors and automatic alerts can aid operators in maintaining the correct balance during loading and unloading. These innovations provide actionable insights, allowing businesses to make informed decisions that streamline their cold chain logistics. By proactively managing weight distribution, companies can reduce downtime and increase the reliability of their temperature-sensitive deliveries.
Furthermore, advancements in software solutions enable comprehensive data analysis regarding weight management. By evaluating historical performance metrics, logistics managers can identify trends and adjust loading practices for improved efficiency. Such data-driven approaches empower businesses to enhance operational strategies while ensuring compliance with safety regulations, ultimately supporting more effective chiller truck tail lift capacity management.
Future Trends in Cold Chain Transportation
Future trends in cold chain transportation are leaning towards enhanced digital integration, where real-time tracking systems provide visibility into the condition and location of temperature-sensitive goods. This innovation helps businesses react swiftly to potential issues during transit, ensuring that products are maintained within required temperature ranges, effectively minimizing spoilage and enhancing overall logistics efficiency.
Automation is also becoming a key feature, with developments in automated tail lift operations streamlining loading and unloading processes. These advancements reduce the manpower needed while increasing precision and speed, thereby improving turnaround times for deliveries in the cold chain sector.
Moreover, sustainability practices are gaining traction, with a focus on energy-efficient technologies in chiller trucks. Businesses are increasingly adopting eco-friendly refrigeration systems and lightweight materials to enhance fuel efficiency, reduce emissions, and maintain compliance with evolving environmental regulations. This shift not only addresses regulatory challenges but also appeals to consumers who prefer environmentally responsible practices.
Case Studies of Successful Implementations
One notable case study showcasing the effective implementation of advanced tail lift technology is a large food distribution company that integrated smart sensors into their chiller truck operations. By utilizing this technology, the company achieved real-time monitoring of load distribution, which directly improved the stability and safety of their deliveries. As a result, the fleet experienced a significant reduction in mechanical failures, allowing for a more reliable transport of temperature-sensitive goods.
Another example involves a pharmaceutical supplier that adopted automated tail lift systems to enhance their loading and unloading processes. These innovations allowed for precise control over weight distribution, minimizing the risk of damage to sensitive medications during transport. The implementation led to improved operational efficiency, reducing delivery times and ensuring that products remained within designated temperature ranges throughout their journey.
A logistics provider specializing in perishable goods employed a combination of lightweight materials and energy-efficient tail lifts, significantly enhancing their vehicles’ overall performance. This strategic move not only improved fuel efficiency but also aligned with the company’s sustainability goals. As a result, the provider successfully reduced operational costs and increased customer satisfaction by consistently delivering high-quality products within required temperature conditions.
Frequently Asked Questions About Chiller Truck Tail Lift Capacity

Understanding chiller truck tail lift capacity involves crucial considerations for operational success. Selecting the right tail lift for specific needs ensures efficiency, while recognizing the signs of overloading is vital for safety. Additionally, maintaining optimal performance through regular upkeep directly impacts the ability to manage temperature-sensitive goods effectively. Each of these topics offers practical insights to enhance logistics operations.
How to Select the Right Tail Lift for Your Chiller Truck
Selecting the right tail lift for a chiller truck begins with understanding the specific weight and size requirements of the cargo. Businesses must consider the total weight capacity needed to transport temperature-sensitive goods, as well as how the load will be distributed across the tail lift. This ensures safe handling and efficient operations during loading and unloading processes.
Next, evaluating the type of tail lift is essential. Different types, such as column lifts or tuckaway lifts, have unique specifications that cater to varying applications. Choosing a tail lift that aligns with the intended use—be it for urban deliveries or heavy machinery transport—can significantly enhance efficiency and safety in cold chain logistics.
Finally, businesses should take into account the compatibility of the tail lift with their chiller truck’s overall design and specifications. A well-integrated tail lift not only improves performance but also contributes to a seamless loading and unloading experience, reducing the time taken for each delivery. Investing time in this selection process helps businesses optimize their operations and maintain the integrity of their temperature-sensitive products.
What Are the Signs of Overloading?
Overloading a chiller truck tail lift can manifest through various telltale signs that operators should recognize promptly. One common indicator is the tail lift operating sluggishly or struggling to raise the load, which suggests that the weight exceeds its designated capacity. Additionally, noticeable creaking or abnormal noises during operation can signal potential strain on the hydraulic system, indicating an overload situation that requires immediate attention.
Another sign of overloading is the instability of the chiller truck during loading or unloading processes. If the vehicle tilts or feels unusually uneven while the tail lift is in use, this may point to uneven weight distribution or excessive load weight. This imbalance could not only complicate operations but also pose significant safety risks to personnel involved in the handling of temperature-sensitive goods.
Lastly, frequent malfunctioning or breakdowns of the tail lift system can be a clear symptom of overloading. Such issues can arise from continual strain on components like the hydraulic cylinder when subjected to loads beyond the specified limits. Regular maintenance and monitoring of load conditions are crucial, as ignoring these signs can lead to costly repairs and negatively impact the efficiency of cold chain logistics.
How to Maintain Optimal Performance?
To maintain optimal performance of chiller truck tail lifts, regular inspections are essential to identify wear and tear in hydraulic components. Routine checks help ensure that all parts function correctly and can handle the demands of transporting temperature-sensitive goods without disruption. Engaging trained technicians for this process can enhance safety and extend the lifespan of the tail lift systems.
Another key aspect of maintaining performance is to adhere to the manufacturer’s guidelines regarding load limits. This not only protects the integrity of the tail lift but also ensures that the truck operates safely during loading and unloading. Operators should strictly monitor payloads to prevent mechanical failures that can arise from overloading.
Finally, periodic maintenance of the hydraulic fluids and lubrication systems is crucial for the efficiency of the tail lift. Keeping these systems well-maintained allows for smoother operation and quicker response times during use. By prioritizing these maintenance practices, businesses can significantly reduce operational downtime and enhance the reliability of their cold chain logistics.
Conclusion
Understanding chiller truck tail lift capacity is essential for the effective transport of temperature-sensitive goods. Proper management of weight limitations enhances operational efficiency and safety, preventing costly breakdowns and ensuring product integrity. By selecting the right tail lift type and adhering to best practices, businesses can significantly improve their cold chain logistics. This knowledge empowers operators to maintain high standards in delivering perishables, pharmaceuticals, and other critical items securely and efficiently.